рос | укр
Головна сторінка
Випадкова сторінка
КАТЕГОРІЇ:
АвтомобіліБіологіяБудівництвоВідпочинок і туризмГеографіяДім і садЕкологіяЕкономікаЕлектронікаІноземні мовиІнформатикаІншеІсторіяКультураЛітератураМатематикаМедицинаМеталлургіяМеханікаОсвітаОхорона праціПедагогікаПолітикаПравоПсихологіяРелігіяСоціологіяСпортФізикаФілософіяФінансиХімія
|
Тема: Поняття про біосферу. Природні та антропогенні забруднення біосфери
Дата добавления: 2015-03-11; просмотров: 587
8. Вывод.
Лабораторная работа № 2
Тема: Свойства металлов и сплавов: углеродистые инструментальные стали.
Тип: применение и совершенствование знаний.
Цель: изучить технологический процесс плавления стали, получаемые сплавы и их свойства; уметь читать диаграмму состояния железоуглеродистых сплавов; рассмотреть свойства придаваемые сплавам легирующими элементами и «вредными» примесями.
Оснащение: учебник Макиенко Н. И. «Слесарное дело с основами материаловедения», тетрадь для лабораторно – практических работ, ручка, карандаш, линейка.
ХОД РАБОТЫ
1. Опишите технологический процесс получения углеродистой стали по конвекторному способу.
2. Каково устройство и работа мартеновской печи?
3. Каково назначение индукционной печи? Перечислите преимущества и недостатки индукционной печи.
4. Зарисовать диаграмму состояния железоуглеродистых сплавов по сталям (с.64, р.26 до 2% С).
5. Запишите состояние сплава и температуру его образования. Какими свойствами обладают образовавшиеся сплавы?
6. Назовите марки стали, которые используют для изготовления молотков, ножовочных полотен, напильников, ножниц?
7. Расшифруйте марки сталей: У10А, У8Г, У9ГА.
8. Вывод.
Лабораторная работа № 3
Тема: Свойства металлов и сплавов: углеродистые конструкционные стали.
Тип: применение и совершенствование знаний.
Цель: изучить устройство и работу электропечей, получаемые сплавы и их свойства; уметь читать диаграмму состояния железоуглеродистых сплавов и расшифровывать марки сталей; рассмотреть свойства придаваемые сплавам легирующими элементами и «вредными» примесями.
Оснащение: учебник Макиенко Н. И. «Слесарное дело с основами материаловедения», тетрадь для лабораторно – практических работ, ручка, карандаш, линейка.
ХОД РАБОТЫ
1. Каково устройство и работа электрической печи?
2. В чём заключается метод электрошлаковой переплавки?
3. Расшифруйте марки сталей: 10кп, 65Г, БСт6, ВКСт4, 0,8.
4. Опишите технологический процесс получения углеродистой стали по бессемеровскому ( томасовскому) способу.
5. Опишите классификацию сталей по группам А; Б; В.
6. Где применяются стали обыкновенного качества и качественные?
7. Вывод.
Лабораторная работа № 4
Тема: Твёрдые сплавы.
Тип: применение и совершенствование знаний.
Цель: изучить получаемые твёрдые сплавы их свойства и состав; уметь читать диаграмму состояния железоуглеродистых сплавов; рассмотреть сплавы получаемые спеканием и литые, соотнести свойства минерало- и металлокерамических сплавов.
Оснащение: учебник Макиенко Н. И. «Слесарное дело с основами материаловедения», тетрадь для лабораторно – практических работ, ручка, карандаш, линейка.
ХОД УРОКА
1. Дайте определение понятию «твёрдые сплавы».
2. Перечислите общие свойства твёрдых сплавов.
3. Для чего и с какой целью используют наплавочные твёрдые сплавы?
4. Дайте характеристику литым сплавам: стеллит и сормайт.
5. Дайте характеристику порошкообразным сплавам: вокар и сталинит.
6. Раскройте понятие «металлокерамические» твердые сплавы.
7. Расшифруйте марки твёрдых сплавов: ВК3; ВК3М; ВК4В; Т30К4; Т5К12В и область их применения.
8. Дайте характеристику минералокерамических сплавов. Область их применения.
9. Вывод.
Лабораторная работа № 5
Тема: Цветные металлы.
Тип: применение и совершенствование знаний.
Цель: изучить применяемые цветные металлы и их сплавы; свойства и состав; уметь читать диаграмму состояния железоуглеродистых сплавов; рассмотреть сплавы получаемые спеканием и литые.
Оснащение: учебник Макиенко Н. И. «Слесарное дело с основами материаловедения», тетрадь для лабораторно – практических работ, ручка, карандаш, линейка.
ХОД УРОКА
1. Перечислите общие свойства цветных металлов на примере меди и алюминия.
2. Каков состав латуни? Её свойства и применение в технике.
3. Расшифруйте марку: ЛС 59-1.
4. Каков состав бронзы? Её свойства и применение в технике.
5. Расшифруйте марку: БрОФ 6,5-0,25; БрОЦС 6-6-3.
6. Свойства дюралюминов. Их разновидности (деформируемые, высокопрочные, литейные).
7. Применение сплавов на основе алюминия и магния.
8. Применение сплавов на основе алюминия и меди.
9. Применение сплавов на основе алюминия и кремния.
10. Какие сплавы относятся к жаропрочным и их применение.
11. Перечислите свойства магниевых и титановых сплавов.
12. Достоинства и недостатки литейных магниевых сплавов.
13. Охарактеризуйте титановые сплавы.
14. Вывод.
Лабораторная работа № 6
Тема: Термическая обработка металла.
Тип: применение и совершенствование знаний.
Цель: изучить понятие «термическая обработка» металла; рассмотреть виды и технологию процесса, применение в производстве; воспитывать чувство ответственности за будущую профессию.
Оснащение: учебник Макиенко Н. И. «Слесарное дело с основами материаловедения» (68-80), тетрадь для лабораторно – практических работ, ручка, карандаш, линейка.
ХОД УРОКА
1. Дайте определение понятию «отжиг», каково его назначение?
2. Используя диаграмму «Оптимальные интервалы нагрева стали для отжига…» (с.68), заполните данные в таблицу № 1:
Таблица № 1
№
| наименование
| назначение
| Температура процесса
| применение
|
| Низкотемпературный
|
|
|
|
| Полный
|
|
|
|
| Неполный
|
|
|
|
| Изотермический
|
|
|
|
| Диффузионный
|
|
|
|
| Зернистый перлит
|
|
|
|
| Рекристаллизация
|
|
|
|
| Нормализация
|
|
|
| 3. Дайте определение понятию «закалка», каково её назначение?
4. Перечислите виды закалочных сред.
5. Используя диаграмму «Оптимальные интервалы нагрева стали для отжига…» (с.68), заполните данные в таблицу № 2:
Таблица № 2
№
| Виды закалки
| Технология
| Применение
| Температура процесса
| Приобретаемые свойства
| Достоинства и недостатки
|
| В одном охладителе
|
|
|
|
|
|
| В двух средах
|
|
|
|
|
|
| Ступенчатая
|
|
|
|
|
|
| С подстуживанием
|
|
|
|
|
|
| Самоотпуском
|
|
|
|
|
|
| Изотермическая
|
|
|
|
|
|
| Патентирование
|
|
|
|
|
| 6. Дайте характеристику поверхностной закалке заполнив таблицу № 3 данными:
Таблица № 3
№
| Виды поверхностной закалки
| Оборудование
| Температурный режим
| Применение
|
| Пламенная
|
|
|
|
| В электролите
|
|
|
|
| Токами высокой частоты
|
|
|
| 7. Какова сущность обработки холодом?
8. Дайте определение понятию «отпуск», каково его назначение?
9. Опишите технологический процесс отпуска в таблице № 4:
Таблица № 4
№
| Низкий отпуск
| Средний отпуск
| Высокий отпуск
|
|
|
|
| 10. В чём заключается сущность процесса старения стали?
11. Вывод.
Лабораторная работа № 7
Тема: Химико-термическая обработка стали.
Тип: применение и совершенствование знаний.
Цель: изучить понятие «химико-термическая» обработка стали, какие виды являются более распространенными, целесообразность их применения; рассмотреть технологию цементации, азотирования, цианирования и диффузной металлизации; воспитывать чувство ответственности за будущую профессию.
Оснащение: учебник Макиенко Н. И. «Слесарное дело с основами материаловедения» (81-86), тетрадь для лабораторно – практических работ, ручка, карандаш, линейка.
ХОД УРОКА
1. Дайте определение понятию «химико-термическая» обработка стали.
2. Дайте определение понятию «цементация», каково её назначение?
3. Что называют карбюризаторами?
4. Охарактеризуйте процесс цементации, заполнив таблицу № 1:
Таблица № 1
№
| Наименование
| цементация
| твёрдая
| жидкая
| газовая
|
| Карбюризатор
|
|
|
|
| Технология процесса
|
|
|
|
| Материалы
|
|
|
|
| «+» «-»
|
|
|
| 5. Дайте определение понятию «азотирование», каково её назначение?
6. Охарактеризуйте процесс азотирования, заполнив таблицу № 2:
Таблица № 2
№
| Наименование
| Азотирование
|
| Оборудование
|
|
| Технология процесса
|
|
| Глубина проникновения
|
|
| Материалы
|
| 7. Дайте определение понятию «цианирование»?
8. Охарактеризуйте процесс цианирования, заполнив таблицу № 3:
Таблица № 3
№
| наименование
| цианирование
| твёрдое
| жидкое
| Высоко
температурное
| Средне
температурное
| Низко
температурное
|
| Карбюризатор
|
|
|
|
|
|
| Приобретаемые свойства
|
|
|
|
|
|
| Материалы
|
|
|
|
|
| 9. Раскройте сущность процесса нитроцементации.
10. Дайте определение понятию «диффузная металлизация», каково её назначение?
11. Охарактеризуйте процесс алитирования, заполнив таблицу № 4:
Таблица №4
№
| наименование
| алитирование
| твёрдое
| жидкостное
| металлизация
|
| Технология процесса
|
|
|
| 12. Охарактеризуйте процесс хромирования, заполнив таблицу № 5:
Таблица № 5
№
| наименование
| хромирование
| твёрдое
| жидкостное
| газовое
|
| Технология процесса
|
|
|
| 13. Вывод.
Лабораторная работа № 8
Тема: Неметаллы. Абразивы. Жидкости.
Тип: применение и совершенствование знаний.
Цель: изучить
Оснащение: учебник Макиенко Н. И. «Слесарное дело с основами материаловедения», тетрадь для лабораторно – практических работ, ручка, карандаш, линейка.
ХОД УРОКА
1. Дайте определение понятию «пластические массы» и опишите их общие свойства.
2. Дайте определение понятию «полимеры».
3. Из перечисленных видов пластмасс выберите те, которые соответствуют свойствам, указанным в таблице № 1.
Пластмассы: фенопласты, аминопласты, полиэфирные, эпоксидные и полиамидные смолы, текстолит, поделочный и электротехнический текстолит, гетинакс, стеклотекстолит, органическое стекло, асбестотекстолит, капрон, нейлон, пенопласт, целлулоид, винипласт.
Таблица № 1
№
| Свойства
| Пластические массы
|
| Способность к окрашиванию
|
|
| Способность к повторной формовке
|
|
| Эластичность
|
|
| Устойчивость к коррозии
|
|
| Устойчивость к воздействию кислот
|
|
| Электропроводность
|
|
| Температурная стойкость
|
|
| Способность к склеиванию
|
|
| Износоустойчивость
|
|
| Хорошее отношение к резанию
|
|
| Хорошее сопротивление трению
|
|
| Высокая прочность на разрыв
|
|
| Низкая гигроскопичность
|
|
| Вязкость при низких температурах
|
|
| Высокие изоляционные показатели
|
|
| Низкая способность к горению
|
|
| Высокая способность к горению
|
| 4. Сообщите основные свойства и состав, которыми обладают материалы и результаты внесите в таблицу № 2:
Таблица № 2
№
| Материалы
| Свойства
| Состав
|
| Резина
|
|
|
| Эбонит
|
|
|
| Водонепроницаемый картон
|
|
|
| Электроизоляционный картон
|
|
|
| Слюда
|
|
|
| Асбест
|
|
|
| Фибра
|
|
|
| Паронит
|
|
|
| Кожа техническая
|
|
|
| Войлок технический
|
|
| | | | | | 5. Дайте характеристику абразивам и результаты занесите в таблицу № 3:
Таблица № 3
Абразивы
| природные
| искусственные
| наименование
| характеристика
| наименование
| характеристика
| Алмаз
|
| Электрокорунд нормальный
|
| Корунд
|
| Электрокорунд белый
|
| Наждак
|
| Карбид кремния
|
| Кварц
|
| Карбид бора
|
| Гранат
|
| Борсиликокарбид
|
|
|
| Синтетический алмаз
|
| 6. Опишите классификацию отечественных масел.
7. Вывод.
ПЕРЕЧЕНЬ ВАРИАНТОВ ДЛЯ РАСЧЕТНОЙ РАБОТЫ
Вариант №1
Вещество
| Состав, % по массе
| MgCL2
| KCL
| NaCL
| MgO
| Mg
| Безводный карналлит
| 48.5
| 42.3
| 5.8
| 3.4
| -
| Отработанный электролит
| 4,6
| 73,0
| 22,12
| 0,28
| -
| Шлам
|
|
| 33,5
|
| 3,5
| Возгон
|
| 31,6
| 25,4
| -
| -
| Магний-сырец
| 0,02
| 0,19
| 0,09
| -
| 99,7
|
Вариант №2
Вещество
| Состав, % по массе
| MgCL2
| KCL
| NaCL
| MgO
| Mg
| Безводный карналлит
|
|
|
|
| -
| Отработанный электролит
| 4,5
|
| 19,3
| 0,2
| -
| Шлам
|
|
|
|
|
| Возгон
|
|
|
| -
| -
| Магний-сырец
| 0,01
| 0,26
| 0,15
| -
| 99,58
|
Вариант №3
Вещество
| Состав, % по массе
| MgCL2
| KCL
| NaCL
| MgO
| Mg
| Безводный карналлит
|
|
|
|
| -
| Отработанный электролит
| 4,2
| 77,2
| 18,4
| 0,2
| -
| Шлам
| 8,5
|
| 15,5
|
|
| Возгон
|
|
|
| -
| -
| Магний-сырец
| 0,03
| 0,3
| 0,2
| -
| 99,47
|
Вариант №4
Вещество
| Состав, % по массе
| MgCL2
| KCL
| NaCL
| MgO
| Mg
| Безводный карналлит
|
|
|
|
| -
| Отработанный электролит
| 5,3
|
| 14,5
| 0,2
| -
| Шлам
|
|
|
|
|
| Возгон
|
|
|
| -
| -
| Магний-сырец
| 0,01
| 0,3
| 0,09
| -
| 99,6
|
Вариант №5
Вещество
| Состав, % по массе
| MgCL2
| KCL
| NaCL
| MgO
| Mg
| Безводный карналлит
|
|
|
|
| -
| Отработанный электролит
| 4,5
|
| 18,4
| 0,1
| -
| Шлам
|
|
|
|
|
| Возгон
|
|
|
| -
| -
| Магний-сырец
| 0,02
| 0,15
| 0,43
| -
| 99,4
|
Вариант №6
Вещество
| Состав, % по массе
| MgCL2
| KCL
| NaCL
| MgO
| Mg
| Безводный карналлит
| 51,0
| 42,0
| 6,0
| 1,0
| -
| Отработанный электролит
| 5,0
| 75,0
| 19,8
| 0,2
| -
| Шлам
| 8,0
| 54,0
| 15,0
| 20,0
| 3,0
| Возгон
| 30,0
| 40,0
| 30,0
| -
|
| Магний-сырец
| 0,02
| 0,28
| 0,10
| -
| 99,6
| Пример расчета.
Введение
При расчете магниевых электролизеров используются показатели промышленных данных. Ниже приведен пример расчета диафрагменного электролизера на 100 кА с верхним вводом анодов для электролиза безводного карналлита.
Исходные данные:
Таблица 1.1.
№
| Параметры
| Ед. изм
| Значения
| 1.
| Сила тока
| кА
|
| 2.
| Плотность тока
| А/см2
|
|
| Анодная Да
|
| 0,41
|
| Катодная Дк
|
| 0,50
|
| Проходная плотность тока в аноде в аноде Да/
|
| 5,2
|
| Проходная плотность тока в катоде Дк/
|
|
| 3.
| Расстояние между электродами
| см
|
| 4.
| Ширина анода Ва
| см
|
| 5.
| Выход по току
| %
|
| 6.
| Выход на 1кг магния-сырца
| кг
|
|
| Шлама
|
| 0,12
|
| Возгона
|
| 0,1
|
| Отработанного электролита
|
| 3,8
| 7.
| Отсос газа из катодных ячеек
| М3/ч
|
|
Состав нагруженного в электролизер сырья и извлекаемых из него веществ:
Вариант №0 Таблица 1.2.
Вещество
| Состав, % по массе
| MgCL2
| KCL
| NaCL
| MgO
| Mg
| Безводный карналлит
| 51,0
| 42,0
| 6,0
| 1,0
| -
| Отработанный электролит
| 5,0
| 75,0
| 19,8
| 0,2
| -
| Шлам
| 8,0
| 54,0
| 15,0
| 20,0
| 3,0
| Возгон
| 30,0
| 40,0
| 30,0
| -
| -
| Магний-сырец
| 0,02
| 0,28
| 0,10
| -
| 99,6
|
ВАРИАНТЫ ДЛЯ РАСЧЕТА
Вариант
| I,кА
| Да, А/см
| Дк, А/см2
| Да, А/см2
| Дк, А/см2
| Nn Mg %
| Nn CI%
| Шлам, кг
| Возгон кг
| Отр. электролит, кг
|
|
| 0,4
| 0,52
| 5,1
| 25,6
|
|
| 0,15
| 0,1
| 3,9
|
|
| 0,41
| 0,51
| 5,0
| 24,0
|
|
| 0,12
| 0,2
|
|
|
| 0,42
| 0,50
| 4,7
| 24,3
|
|
| 0,14
| 0,3
| 3,92
|
|
| 0,43
| 0,53
| 4,8
| 25,1
|
|
| 0,11
| 0,15
| 3,8
|
|
| 0,39
| 0,50
| 5,2
| 23,7
|
|
| 0,15
| 0,25
| 3,85
|
|
| 0,38
| 0,48
| 4,9
| 25,8
|
|
| 0,12
| 0,2
|
|
|
| 0,37
| 0,43
| 5,2
| 25,2
|
|
| 0,13
| 0,3
| 3,95
|
|
| 0,39
| 0,52
| 4,8
| 24,5
|
|
| 0,12
| 0,12
| 3,9
|
|
| 0,42
| 0,49
| 4,7
| 24,8
|
|
| 0,15
| 0,1
| 3,9
|
|
| 0,40
| 0,47
| 5,0
| 24,9
|
|
| 0,12
| 0,2
| 3,93
|
|
| 0,38
| 0,49
| 5,1
| 24,5
|
|
| 0,14
| 0,3
| 3,95
|
|
| 0,41
| 0,51
| 4,8
| 25,5
|
|
| 0,11
| 0,15
|
|
|
| 0,37
| 0,50
| 5,1
| 24,4
|
|
| 0,15
| 0,25
| 3,85
|
|
| 0,42
| 0,53
| 4,7
| 25,6
|
|
| 0,12
| 0,2
|
|
|
| 0,43
| 0,52
| 5,2
| 24,3
|
|
| 0,13
| 0,3
| 3,85
|
|
| 0,39
| 0,48
| 4,9
| 25,8
|
|
| 0,12
| 0,12
| 3,87
|
|
| 0,41
| 0,49
| 4,8
| 25,3
|
|
| 0,15
| 0,1
| 3,9
|
|
| 0,37
| 0,48
| 5,0
| 24,1
|
|
| 0,12
| 0,2
|
|
|
| 0,38
| 0,50
| 5,1
| 23,8
|
|
| 0,14
| 0,3
| 3,92
|
|
| 0,37
| 0,52
| 5,2
| 25,5
|
|
| 0,11
| 0,15
| 3,94
|
|
| 0,42
| 0,54
| 4,9
| 24,9
|
|
| 0,15
| 0,25
| 3,96
|
|
| 0,40
| 0,53
| 4,7
| 24,1
|
|
| 0,12
| 0,3
| 3,99
|
|
| 0,43
| 0,51
| 4,8
| 25,0
|
|
| 0,13
| 0,12
| 3,8
|
|
| 0,39
| 0,49
| 4,7
| 25,3
|
|
| 0,12
| 0,1
|
|
|
|
| 0,50
| 5,0
| 24,9
|
|
| 0,13
| 0,2
| 3,85
|
|
|
|
|
|
|
|
|
|
|
|
ПРИМЕР РАСЧЕТА МАГНИЕВОГО ЭЛЕКТРОЛИЗЕРА
| Материальный баланс
1.В расчет материального баланса входит определение количеств исходного сырья и продуктов, полученных в результате процесса электролиза.
Производительность электролизера определяем согласна закону Фарадея:
P=0.454*I*nt
P- производительность электролизера (кг/ч)
) I-сила тока (А)
nt-выход тока, (доли единиц)
0,454-электрохимический эквивалент магния, (г/А*ч)
При электролизе за час работы электролизера выделяется магния:
1.В состав магния-сырца:
P=0,454*100*0,8=36,3 кг/ч
2.В состав шлама:
36,3*0,12*0,03=0,13 кг/ч
Где 0,12-выход шлама (таблица 1.1)
0,03-содержания магния (таблица 1.2)
Всего: 36,3+0,13=36,43 кг/ч
Извлекается из электролизера (кг/ч):
Магний-сырца 36,43:0,996=36,5 кг
Где 0,996-содержание магния в магнии-сырце, (доли единиц)(таблица 1.2.)
Шлама 36,5*0,12=4,38
Где 0,12-выход шлама (кг) (таблица 1.1.)
Возгона 36,5*0,10=3,65 кг
Где 0,10-выход возгона (кг) (таблица 1.1)
Отработанного электролита 36,5*3,8=138,7
Где 3,8-выход отработанного электролита (кг) (таблица 1.1.)
Хлора 100*1,323*0,8=105,84
Где 100-сила тока (кА)
1,323-электрохимический эквивалент хлора (г/А*ч)
0,8-выход по току, (доли единиц)
Часовой расход безводного карналлита составляет:
36,5+4,38+3,65+138,7+105,84=289 кг
Расход безводного карналлита (51% MgCI2) на 1кг магния-сырца:
289KCI*MgCI2 36.5 Mg
Х кг 1 кг
289*1/36,5=7,93 кг
Результаты расчета сведены в таблицу.2
Материальный баланс магниевого электролизера на 100 кА
Поступает в электролизер
| Извлекается из электролизера
| Сырье
| На 1000кг сырья
| Кг/ч
| Продукты
| На 1000кг сырья
| Кг/ч
| Безводный карналлит 51% MgCI2
|
|
| Магний- сырец (99,6%Mg)
| 126,2
| 36,5
| Отработанный электролит
| 481,5
| 138,7
| Шлам
| 15,2
| 4,38
| Возгон
| 12,6
| 3,65
| Хлор (100%CI2)
| 264.5
| 105.84
| Всего
|
|
| Всего:
|
|
|
Наряду с основными процессами происходит ряд побочных.
Например: в карналлитовом электролите частично хлорируется оксид магния.
За 1 час в электролизере поступает оксид магния в составе безводного карналлита.
289*0,01=2,89 кг
Где 0,01-содержания MgO в безводном карналлите, (доли единиц).(Таблица 1.2.)
За это же время из электролиза извлекаются оксид магния (в составе отработанного электролита и шлама) (Таблица 2 и таблица 1.2.)
138,7*0,002+4,38*0,2=1,25 кг
При хлорирование MgO расходуется некоторое количество хлора, что уменьшает его выход, и образуется дополнительное количество хлорида магния, используемого для электролиза.
Степень хлорирования оксида магния:

При хлорировании оксида магния получается хлорида магния:
(2,89-1,25)*2,36=3,76 кг/ч
Где 2,36-отношение молекулярных масс MgCI2 и МдО
Расходуется хлора:
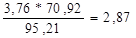
Где 70,92 и 95,21-соответсвенно молекулярные массы хлора и хлорида магния
| Материальный баланс
1.В расчет материального баланса входит определение количеств исходного сырья и продуктов, полученных в результате процесса электролиза.
Производительность электролизера определяем согласна закону Фарадея:
P=0.454*I*nt
P- производительность электролизера (кг/ч)
) I-сила тока (А)
nt-выход тока, (доли единиц
0,454-электрохимический эквивалент магния, (г/А*ч)
При электролизе за час работы электролизера выделяется магния:
1.В состав магния-сырца:
P=
2.В состав шлама:
= кг/ч
Всего:
Извлекается из электролизера (кг/ч):
Магний-сырца
Шлама
Возгона
Отработанного электролита
Хлора
Часовой расход безводного карналлита составляет:
Расход безводного карналлита (51% MgCI2) на 1кг магния-сырца:
KCI*MgCI2 Mg
Х кг 1 кг
Результаты расчета сведены в таблицу.2
Материальный баланс магниевого электролизера на кА
Поступает в электролизер
| Извлекается из электролизера
| Сырье
| На 1000кг сырья
| Кг/ч
| Продукты
| На 1000кг сырья
| Кг/ч
| Безводный карналлит
% MgCI2
|
|
| Магний- сырец
( %Mg)
|
|
| Отработанный электролит
|
|
| Шлам
|
|
| Возгон
|
|
| Хлор ( 100 %CI2)
|
|
| Всего
|
|
| Всего:
|
|
|
Наряду с основными процессами происходит ряд побочных.
В карналлитовом электролите частично хлорируется оксид магния.
За 1 час в электролизере поступает оксид магния в составе безводного карналлита.
= кг
За это же время из электролиза извлекаются оксид магния (в составе отработанного электролита и шлама):
При хлорирование MgO расходуется некоторое количество хлора, что уменьшает его выход, и образуется дополнительное количество хлорида магния, используемого для электролиза.
Степень хлорирования оксида магния:
При хлорировании оксида магния получается хлорида магния:
Расходуется хлора:
| 2.Конструктивный расчет.
А) расчет анодов.
Площадь поверхности сечения всех анодов ровна
S= I: Дa/
Где S-площадь поперечного сечения, см2
I-сила тока, (А)
Дa! а-проходная плотность в аноде (А/см2)
S=100000/5.2=19250 cм2
Для изготовления анодов применяем графитовые брусья поперечным сечением 20х30 см.
Определим расчетное число брусьев во всех анодах:
Принимаем 5 анодов по 7 брусьев в каждом.
Фактическая плотность тока в аноде
Что соответствует принятой плотности тока.
Принимая рабочую высоту анода На=90 см, определим величину рабочей поверхности анода:
Sa=Ha*Ba
Где Ва- ширина анода, (см) (20*7=210)
Sa=90*210=18900 см2
Б) Расчет Катодов
Величина рабочей поверхности катода определяется соотношением анода и катодной плотностей тока:
Где Да-анодная плотность тока, (А/см2)
Дк- катодная плотность тока, (А/см2)
Найдем высоту катодного листа, учитывая. что ширина катода равна ширине анода:
Нк=15500/210 =74 см
Число катодов больше в два раза числа анодов по особенности конструкции: 5*2=10
| 2.Конструктивный расчет.
А) расчет анодов.
Площадь поверхности сечения всех анодов ровна
S= I: Дa/
Где S-площадь поперечного сечения, см2
I-сила тока, (А)
Дa! а-проходная плотность в аноде (А/см2)
S=
Для изготовления анодов применяем графитовые брусья поперечным сечением 20х30 см.
Определим расчетное число брусьев во всех анодах:
m=
Фактическая плотность тока в аноде
Да =
Принимая рабочую высоту анода На= см, определим величину рабочей поверхности анода:
Sa=Ha*Ba
Sa=
Б) Расчет Катодов
Величина рабочей поверхности катода определяется соотношением анода и катодной плотностей тока:
Где Да-анодная плотность тока, (А/см2)
Дк- катодная плотность тока, (А/см2)
sk=
Найдем высоту катодного листа, учитывая, что ширина катода равна ширине анода:
Нк=
Число катодов больше в два раза числа анодов по особенности конструкции:
| 3.Расчет напряжения.
Баланс напряжения электролизера определяется равенством: (В)
U=Va+Vk+Vэ+Vош+Е
Где U-напряжения электролизера,
Va-перепад напряжения в аноде
Vk- перепад напряжения в катоде
Vэ-перепад напряжения в электролите
Vош- перепад напряжения в ошиновке
Е-напряжения разложения
Перепад напряжения в аноде:
Va=Д!а*Lа*pгр
Где Д /а- проходная плотность тока в аноде ,(А/см2)
Lа- путь тока по аноду, Lа=140 см
pгр- удельное сопротивление искусственного графита,11,5х10-4 Ом*см
Va=4,76х140х11,5х10-4=0,77 В
Перепад напряжения в катоде:
Vk=Дk*lk*pст
Где Дk-проходная плотность тока в катоде
lk- пусть тока по катоду,170 см
pст –удельное сопротивление стали при 5000 С ,(0,6*10-4 Ом*см)
Vk=25*170*0.6*10-4=0.26 B
Перепад напряжения в электролите вычисляем по формуле
V=Д ср*L
K*k
Где Д ср= –плотность тока в среднем сечении электролита, (А/см2)
L-расстояние между электродами, (см) (Таблица 1.1.)
K-удельная электропроводимость электролита, К=1,83 0м-1 *см-1
K=коэффициент уменьшения электропроводимости электролита в следствии газонаполнения, К=0,93
Падение напряжения в ошиновке Vош принимаем. Согласно практическим данным=0,3В
Напряжение разложения Е=2,8В
Напряжения на зажимах электролизеров.
U=0.77+0.26+1.85+0.3+2.8= 5,98 B
| 3.Расчет напряжения.
Баланс напряжения электролизера определяется равенством:
U=Va+Vk+Vэ+Vош+Е
Где U-напряжения электролизера, (В)
Va-перепад напряжения в аноде (В)
Vk- перепад напряжения в катоде (В)
Vэ-перепад напряжения в электролите
Vош- перепад напряжения в ошиновке
Е-напряжения разложения
Перепад напряжения в аноде:
Va=Д!а*Lа*pгр
Где Д /а- проходная плотность тока в аноде ,(А/см2)
Lа- путь тока по аноду, Lа=140 см
pгр- удельное сопротивление искусственного графита,11,5х10-4 Ом*см
Va=
Перепад напряжения в катоде:
Vk=Дk*lk*pст
Где Дk-проходная плотность тока в катоде
lk- пусть тока по катоду,170 см
pст –удельное сопротивление стали при 5000 С ,(0,6*10-4 Ом*см)
Vk=
Перепад напряжения в электролите вычисляем по формуле
V=Д ср*L
K*k
Где Д ср= –плотность тока в среднем сечении электролита, (А/см2)
L-расстояние между электродами, (см) (Таблица 1.1.)
K-удельная электропроводимость электролита, К=1,83 0м-1 *см-1
K=коэффициент уменьшения электропроводимости электролита в следствии газонаполнения, К=0,93
V=
Падение напряжения в ошиновке Vош принимаем. Согласно практическим данным=0,3В
Напряжение разложения Е=2,8В
Напряжения на зажимах электролизеров
.
U=
| 4.Тепловой расчет.
Тепловой расчет заключается в составлении теплового равновесия, т.е
Qприхода = Qрасхода
Расчет ведем, принимая температуру процесса 7000 С по уравниванию:
I*V*860=Qр+Qн +Qи+Qпр+Qко +Qтп
Где I-сила тока.(кА)
V- перепад напряжения между электродами, (В)
Qр+Qн +Qи+Qпр – соответственно расход тепла на разложение хлористого магния, нагревание загруженных веществ, испарение электролита и разложение примесей, (ккал/час)
Qко +Qтп– соответственно тепловые потери с газами катодного отсоса из поверхности электролизера, (ккал/час)
А) Приходная часть баланса.
Приход тепла от подведенной электроэнергии
N= 860*I*Vа.к
Va.k =U - Vони
Va.k =5,98-0,3=5,68В
N=100*5.68*860=488480 ккал/ч
Б)Расходная часть баланса.
1.Расход тепла на разложение хлорида магния:
Qp=a md*(H700+H700/)-ax*cx (tэ-tх)
Где - a md количество получаемого в составе магния-сырца и шлама маталлического магния, (кг\ч)
Ах – количество хлора, (кг/ч) (таблица 2.)
H700-удельная теплота образования MgCI2 при 7000C отнесенная к 1кг магния (ккал\кг)
Н700/ -удельная теплота образования KCl*MgCl2 ghb 7000C
CX – теплоемкость хлора, (ккал/кг град)
(tэ-tх)-соответственно температуры хлора в момент выделения и на выходе (С)
Qp= 36.43*(5866+331)-105.84*0.1276*(700-300)=213491 ккал/ч
2.расход тепла на нагревание загруженного безводного карналлита.
Qh=ak*ck (tэ-tк)
Где а- количество загружаемого безводного карналлита, (кг\ч) (таблица 2)
ck- удельная теплоемкость жидкого безводного карналлита, (ккал/кг.град)
(tэ-tк)- соответственно температура электролита и безводного карналлита.(С0)
QH=289*0.266(700-680)=1537 ккал/ч
3.Расход тепла на испарение электролита.
Qu=∑Bqu
Где В-количество соли в возгоне ,(кг/ч)
qu- теплота испарения соли,(ккал/ч)
Согласно материальному балансу, за 1 час получается 3,65 кг возгона, в том числе 1,10 кг MgCI2 1.46 кг KCI и 1.10 NACI (таблица 1.2.)
Qпр= 1.10*344+1.46*530+110*702=1924 ккал/ч
4.Расход тепла на разложение примесей.
Согласно практическим данным, расход тепла по этой статье составляет в среднем 14,5 ккал на 1 кг безводного карналлита.
Qпр=289*14,5=4191 ккал/ч
5.Потери тепла с воздухом, отсасываемым из катодного пространства,(м/ч)
Qk.o=aв*cв(tг-tв)
Где ав - количество воздуха, отсасываемого из катодного пространства (м3 /ч)
Cв - теплоемкость воздуха, (ккал/м3 град)
(tв-tг) - соотвественно температура воздуха на входе в электролизер и на выходе из него, С0
Qk.o=1220*0,31(270-20)=93000 ккал/ч
6.Потери тепла с поверхности электролизера:
Qт.п =N-∑Q
Qт.п=488480-(213491+1537+1924+4191+93000)=174337 ккал/ч
Результаты расчета сводим в таблицу
Приход тепла
| Количество
| Расход тепла
| Количество
| кВт г/ч
| Ккал/ч
| %
| кВт г/ч
| Ккал/ч
| %
| Электрическая энергия
|
|
|
| На разложение хлорида магния
| 248,8
|
| 43,8
|
|
|
|
| На нагревание карналлита безводного
| 1,8
|
| 0,3
|
|
|
|
| На испарение электролита
| 2,2
|
| 0,4
|
|
|
|
| На разложение примесей
| 5,2
|
| 0,9
|
|
|
|
| Тепловые потери: с газами катодного отсоса
|
|
| 19,0
|
|
|
|
| С поверхностью электролизера
|
|
| 35,6
|
Всего:
|
|
|
| Всего:
|
|
|
|
| 4.Тепловой расчет.
Тепловой расчет заключается в составлении теплового равновесия, т.е
Qприхода = Qрасхода
Расчет ведем, принимая температуру процесса 0 С по уравниванию:
I*V*860= Qр+Qн +Qи+Qпр+Qко +Qтп
Где I-сила тока.(кА)
V- перепад напряжения между электродами, (В)
Qр+Qн +Qи+Qпр – соответственно расход тепла на разложение хлористого магния, нагревание загруженных веществ, испарение электролита и разложение примесей, (ккал/час)
Qко +Qтп– соответственно тепловые потери с газами катодного отсоса из поверхности электролизера, (ккал/час)
А) Приходная часть баланса.
Приход тепла от подведенной электроэнергии
N=
Va.k =U - Vони
Va.k =
N=
Б)Расходная часть баланса.
1.Расход тепла на разложение хлорида магния:
Qp=a md*(H700+H700/)-ax*cx (tэ-tх)
Где - a md количество получаемого в составе магния-сырца и шлама маталлического магния, (кг\ч)
Ах – количество хлора, (кг/ч) (таблица 2.)
H700-удельная теплота образования MgCI2 при 7000C отнесенная к 1кг магния (ккал\кг)
Н700/ -удельная теплота образования KCl*MgCl2 ghb 7000C
CX – теплоемкость хлора, (ккал/кг град)
(tэ-tх)-соответственно температуры хлора в момент выделения и на выходе (С)
Qp=
2.расход тепла на нагревание загруженного безводного карналлита.
Qh=ak*ck (t-t)
Где а- количество загружаемого безводного карналлита, (кг\ч) (таблица 2)
ck- удельная теплоемкость жидкого безводного карналлита, (ккал/кг.град)
(t-t)- соответственно температура электролита и безводного карналлита.(С0)
Qh=
3.Расход тепла на испарение электролита.
Qu=∑Bqu
Где В-количество соли в возгоне ,(кг/ч)
Q- теплота испарения соли,(ккал/ч)
Согласно материальному балансу, за 1 час получается кг возгона, в том числе кг MgCI2 кг KCI и кг NACI
Qпр=
4.Расход тепла на разложение примесей.
Согласно практическим данным, расход тепла по этой статье составляет в среднем 14,5 ккал на 1 кг безводного карналлита.
Qпр=
5.Потери тепла с воздухом, отсасываемым из катодного пространства,(м/ч)
Qk.o=aв*cв(tг-tв)
Где ав - количество воздуха, отсасываемого из катодного пространства (м3 /ч)
Cв - теплоемкость воздуха, (ккал/м3 град)
(tв-tг) - соотвественно температура воздуха на входе в электролизер и на выходе из него, С0
Qk.o=
6.Потери тепла с поверхности электролизера:
Qт.п =N-EQ
Qт.п=
Результаты расчета сводим в таблицу
Приход тепла
| Количество
| Расход тепла
| Количество
| кВт г/ч
| Ккал/ч
| %
| кВт г/ч
| Ккал/ч
| %
| Электрическая энергия
|
|
|
| На разложение хлорида магния
|
|
|
|
|
|
|
| На нагревание карналлита безводного
|
|
|
|
|
|
|
| На испарение электролита
|
|
|
|
|
|
|
| На разложение примесей
|
|
|
|
|
|
|
| Тепловые потери: с газами катодного отсоса
|
|
|
|
|
|
|
| С поверхностью электролизера
|
|
|
|
Всего:
|
|
|
| Всего:
|
|
|
|
| 5.Расчет показателей процесса электролиза.
Выход по энергии рассчитывают по формуле:
Где ήэн - выход по энергии(%)
U- напряжение на электролизере (В)
ήт - выход по току.(доли единиц)
Выход энергии без учета потери энергии в ошиновке:
ήэн=3.1/5,68 *0.8*100=43.5%
С учетом потери энергии в ошиновке
ήэн =3.1/5,98 *0.8*100=41,5%
Удельный расход электрической энергии на зажимах электролизера.
Согласно формуле равен:
Wy=5.98/0,454*0.8=16.5 кВт ч./кг
Выход магния на 1 кВт. Ч затраченной электроэнергии
Amd =1000/16,5 *0.996=60.3 г
| 5.Расчет показателей процесса электролиза.
Выход по энергии рассчитывают по формуле:
Где ήэн - выход по энергии(%)
U- напряжение на электролизере (В)
ήт - выход по току.(доли единиц)
Выход энергии без учета потери энергии в ошиновке:
ήэн =
С учетом потери энергии в ошиновке
ήэн =
Удельный расход электрической энергии на зажимах электролизера.
Согласно формуле равен:
Wy=
Выход магния на 1 кВт. Ч затраченной электроэнергии
Amd =
|
Министерство образования и науки Красноярского края
КГБОУ СПО «Красноярский индустриально-металлургический техникум»
Министерство образования и науки Красноярского края
КГБОУ СПО «Красноярский индустриально-металлургический техникум»
1 | <== 2 ==> | 3 | 4 | |